-
Impulses
- Portfolio
-
Career
-
Company
-
Calibration
Foundation of HIGHVOLT
After the reunification, Siemens AG took over the site and equipment of the former VEB Transformatoren- und Röntgenwerk (TuR). Siemens purchased the land and started a step-by-step process of consolidating certain areas of the business. As part of this, the converter construction segment was sold to the company RITZ and the medical technology activities were relocated to Erlangen. After four years under SIEMENS, a review of market activities showed that continued success for such a niche product would only be possible with close customer contact and a neutral company name.
Accordingly, HIGHVOLT was founded in 1995 as a new home for the high-voltage testing technology branch of the company. In the following years, HIGHVOLT not only invested in the construction of a new office building and new production halls to modernize the infrastructure and bring the company up to date with new corporate requirements, but also forged ahead with efforts to further develop its product range to future-proof the site. Joining forces with Maschinenfabrik Reinhausen from Regensburg/Germany meant that HIGHVOLT had a strong and powerful partner by its side that could offer crucial support. Thanks to the close cooperation, it was possible to take optimal advantage of synergy effects across the entire Reinhausen Group.
Well prepared for the future
Well prepared for the future
Continuing the tradition of Koch & Sterzel, TuR and Siemens, a great deal of time and effort went into new developments throughout the three decades under the HIGHVOLT name. But here, the focus was always on the customer – with a systematic and consistent approach to ensuring that the needs of customers and the market are always met. With this customer-focused approach, HIGHVOLT has set standards and is the market leader for, among other things, the use of state-of-the-art power electronics to feed high-voltage testing systems. HIGHVOLT looks ahead into a future shaped by globally rising energy demands. A new production site was opened in Klipphausen in August of this year to meet the growing demand for modern high-voltage testing systems. At the sites in Dresden and Klipphausen, HIGHVOLT will continue to develop innovative solutions over the coming years that will help create safe and sustainable energy supply solutions for the future.
Examples of new devolopments and advancements
CABLES
- Development and production of plunging core reactors
- Variable-frequency resonance testing systems for flexible cable testing
- Continuous development and refinement of mobile cable testing technology
- XXL reactors for testing of particularly long cables
- Offshore testing systems
TRANSFORMERS
- Replacement of motor/generator sets with infeed from power electronics
- Fully automatic testing systems for distribution transformers with integrated data processing
- Complex testing systems with 1, 2 and 3-phase test transformers, synthetic testing systems with fully automatic capacitor banks
DC VOLTAGE TESTING SYSTEMS
- Development of modular testing systems for flexible applications
MEASUREMENT TECHNOLOGY
- Further development of measurement technology, including partial discharge measurement systems
- LiMOS - power loss measurement system
- HiRES - transient recorder for precise recording of key electrical parameters
- HiMON - continuous cable monitoring system
CONTROL TECHNOLOGY
- HiCOS Plus - control system and software for optimization of test sequences
- Digitalization of the complete testing process
- Condition and status monitoring for systems
- Measurement data acquisition for analysis and evaluation of test results
Outstanding product developments
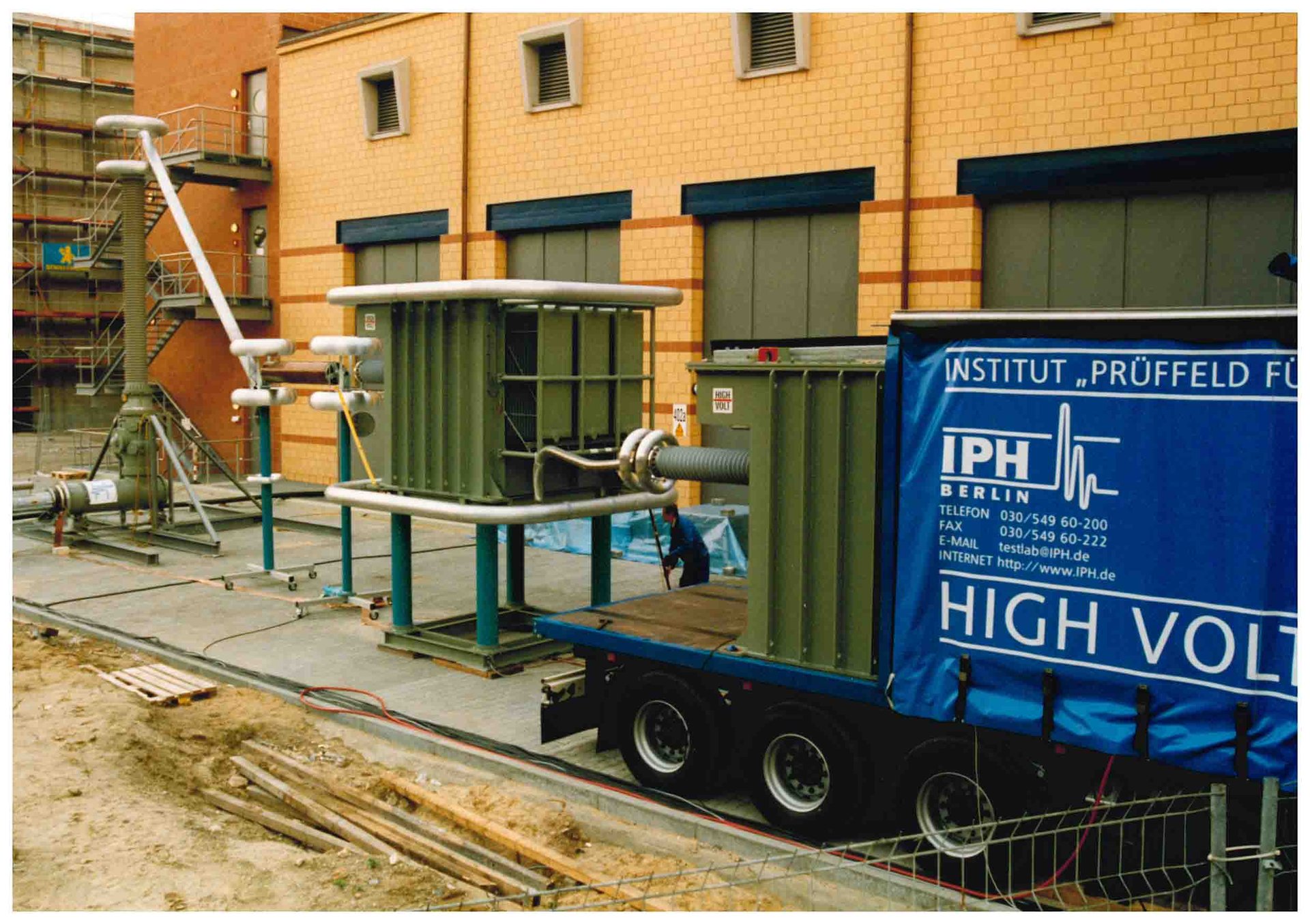
Since the start of the 1990s, cable resonance testing has become established as the globally accepted technology standard, and this has largely been driven by the work done by HIGHVOLT. Mobile testing systems for on-site testing are one of the unique selling points of HIGHVOLT. At present, more than 320 mobile WRV-T systems are in use, and this number is set to continue to grow.
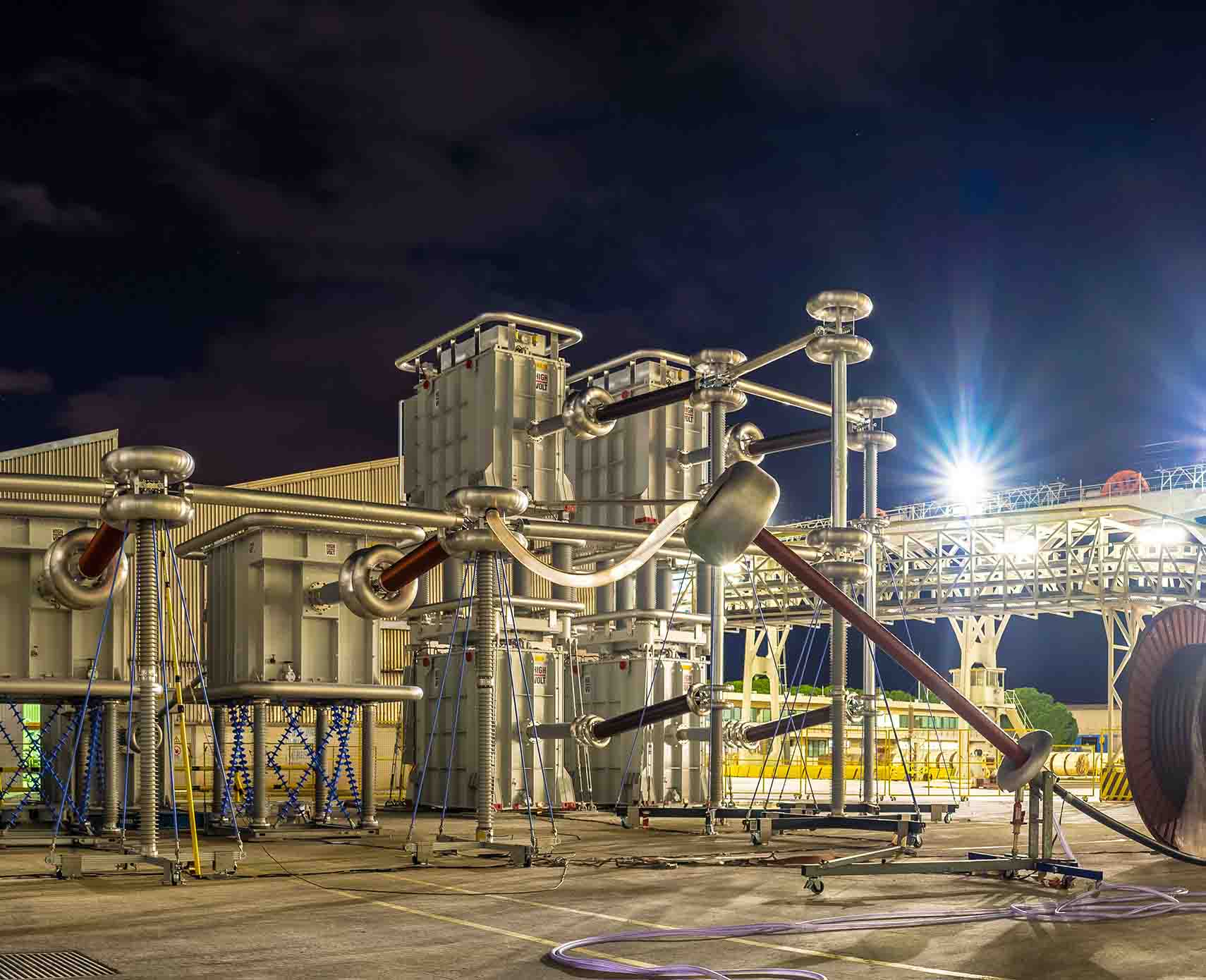
Increasing cable lengths mean demand for greater testing power – and this can be delivered with so-called XXL rectors. Here, by doubling the volume HIGHVOLT has been able to quadruple the testing power.
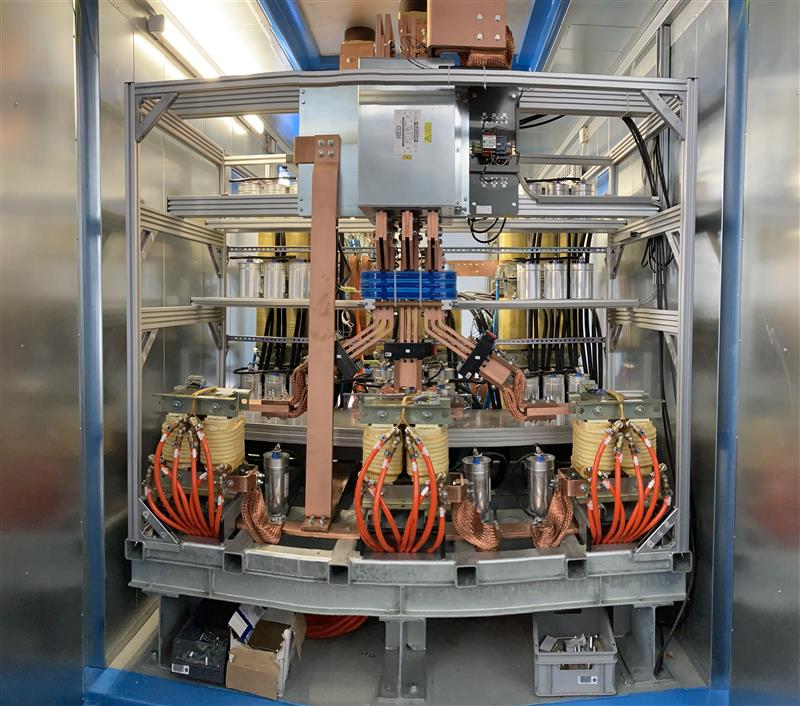
Another great innovation from HIGHVOLT is the way it has managed to establish power electronics as the standard method for providing a supply to complex testing systems. Thanks to this new approach, conventional motor/generator sets can be replaced with a compact and flexible solution inside a container. Typical applications are testing systems for transformers. The latest generation under the name EPS can generate test voltages across a wide frequency range, and thanks to filter technologies developed in-house, these can also be used for sensitive partial discharge measurements on the test object.
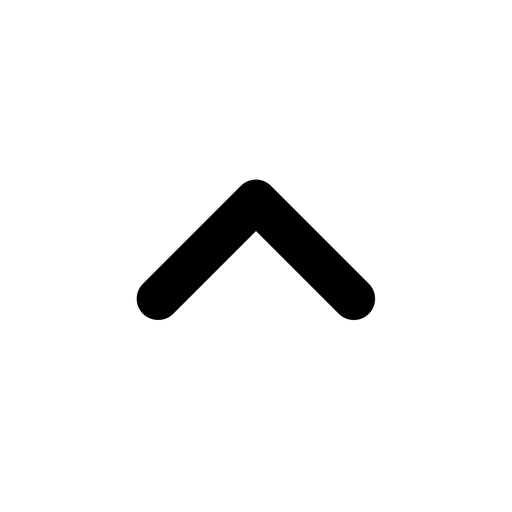
We are here for you. Wherever you are.
Looking for the right contact partner?
Do you have a concern, but don't know whom you should contact? You will find that information in our contact overview. That's a promise.